
- This event has passed.
Online Lecture by prof. Anthony D. Rollett
Synchrotron x-ray Diffraction, Visualisation & Microscopy Combined with Simulation and Machine Learning
March 20 @ 11:30 – 12:30 CET
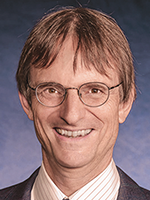
University Professor and US Steel Professor of Metallurgical Engineering & Materials Science
Department of Materials Science & Engineering
Carnegie Mellon University, Pittsburgh
Title:
Synchrotron x-ray Diffraction, Visualisation & Microscopy Combined with Simulation and Machine Learning.
Abstract:
Additive manufacturing (AM), aka 3D printing is a relatively new technology that has given rise to the “maker culture” and an intense interest in design. That has carried over into metals AM, which has jumped almost immediately into manufacturing of actual parts in a variety of alloys. In doing so it has liberated thinking about part design albeit within certain constraints and complex components have been deployed that were previously inaccessible.
One example is described of the co-design of HX against printing constraints, alongside evolution in alloy choice. Another example is the development of a digital twin for processing-microstructure-fatigue in 3D printed metals. These practical applications expose the issue that the reliability of parts that must carry load depends on the internal micro-structure, acutely so in fatigue loading.
This motivates detailed study of all aspects of materials microstructure ranging from precipitation to defects to strain, all of which is ideally suited to the use of intense sources of high energy x-rays as only advanced light sources can deliver. High speed, high resolution diffraction microscopy in stainless steel, alloy 718 and Ti-6Al-4V reveals unexpected solidification and precipitation sequences. High energy diffraction microscopy (HEDM) reveals the highly strained nature of printed metals and how microstructure and internal strain state evolves during subsequent annealing and/or annealing. High speed radiography reveals even more crucial details of how laser light generates vapor cavities that can deposit voids past a critical instability point. “Hot” cracking has been imaged as it happens during the solidification process, which offers the possibility finding printing recipes for alloys previously considered off-limits to 3D printing. Computed tomography (CT) has revealed the presence of porosity in all additively manufactured metals examined to date and confirmed that appropriate process control can limit it. CT has also provided data on surface condition which directly affects fatigue performance.
Permeating all these activities is direct simulation and machine learning as an invaluable aid to the researcher. Pores, for example, need to be understood in terms of their size, location, shape and the stress+strain concentrations that occur under load. Direct simulation with elasto-viscoplastic micro-mechanics with crystal plasticity can be done with good efficiency but need to re-formulated as a reduced-order model for efficient use in workflows that can efficiently evaluate process variations in a digital twin.
This session was chaired by Prof. Leo Kestens (UGent – TU Delft)